
Flare systems at offshore production platforms, refineries and chemical plants are primarily installed for safety purposes. The flare systems are mainly activated due to an unexpected shut-down or when it becomes necessary to suddenly dispose of large amounts of gas.
The effect of gas emission as both an environmental and an economical issue is increasing in importance amongst operators and oil companies. In addition to the obvious safety purposes of a flare, national legislation in more and more countries requires control of the emission, and in some countries operators have to pay taxes for their CO2 emission.
Oil production platforms are nowadays both designed and rebuilt for zero flare gas emission. This change in operation of the flare systems has also influenced on the requirements of the flare gas metering systems. From a continuous, more or less steady flowing amount of flare gas, today's picture is more with the gas flow either to be approximately zero, or at the specified maximum rate.
From an operator's point of view, there is no reason to measure the flare gas unless it is of economical benefit or it is required, for example, for tax payment purposes. In order to achieve economical benefit of a flare gas measurement, the purpose of the measurement could be to identify points of leakage, to obtain better control with emission rates or mass balancing. These application areas for ultrasonic gas flow meters have added metering requirements beyond the direct flare gas metering requirements. Also, this has opened a new market within refineries and onshore process plants.
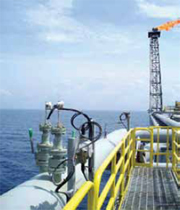
Ultrasonic flow measurement, the ideal technology for Flare gas applications, is independent of gas properties and does not interfere with the flow in any way. All-metal ultrasonic transducers installed in the pipe send ultrasonic sound pulses upstream and downstream through the gas.
From the difference in these transit times between the transducers, with and against the flow, the onboard processor uses advanced signal processing and correlation detection techniques to calculate velocity, and volumetric and mass flow rate.
Temperature and pressure inputs enable the meter to calculate standard volumetric flow. For maximum accuracy, use the two-channel version and measure along two different paths at the same location. The two-channel meter can also measure the flow in two separate pipes or at two different places on the same pipe.
The Flaregas flowmeter has no moving parts to clog or wear out. Its ultrasonic transducers are constructed of titanium or other metals that with stand the corrosive environment usually found in flare gas applications (HF, H2S etc). The transducers are designed for use in hazardous locations.
Wide range-ability allows measurement of flow rate from 0.03 to over 85m/s. (above this usually only happens with a major plant upset and then what is going down the flare line is quantifiable).
In stark contrast to thermal flowmeters, the ultrasonic transit-time technique does not depend on the heat transfer coefficient of the flare gas and does not require regular maintenance. These and other features make the Ultrasonic Flaregas flowmeter unique among flare gas measurement systems.
The flowmeter system consists of a pair of transducers for each channel, preamplifiers, and an electronics console. The transducers can be installed as part of a flow-cell, or directly into the pipe with a hot- or cold-tapping procedure. The electronics console of the Flaregas meter can be located up to 300 m from the transducers.
Click the following links to see product datasheets:
Fluenta Datasheet
Panametrics Datasheet